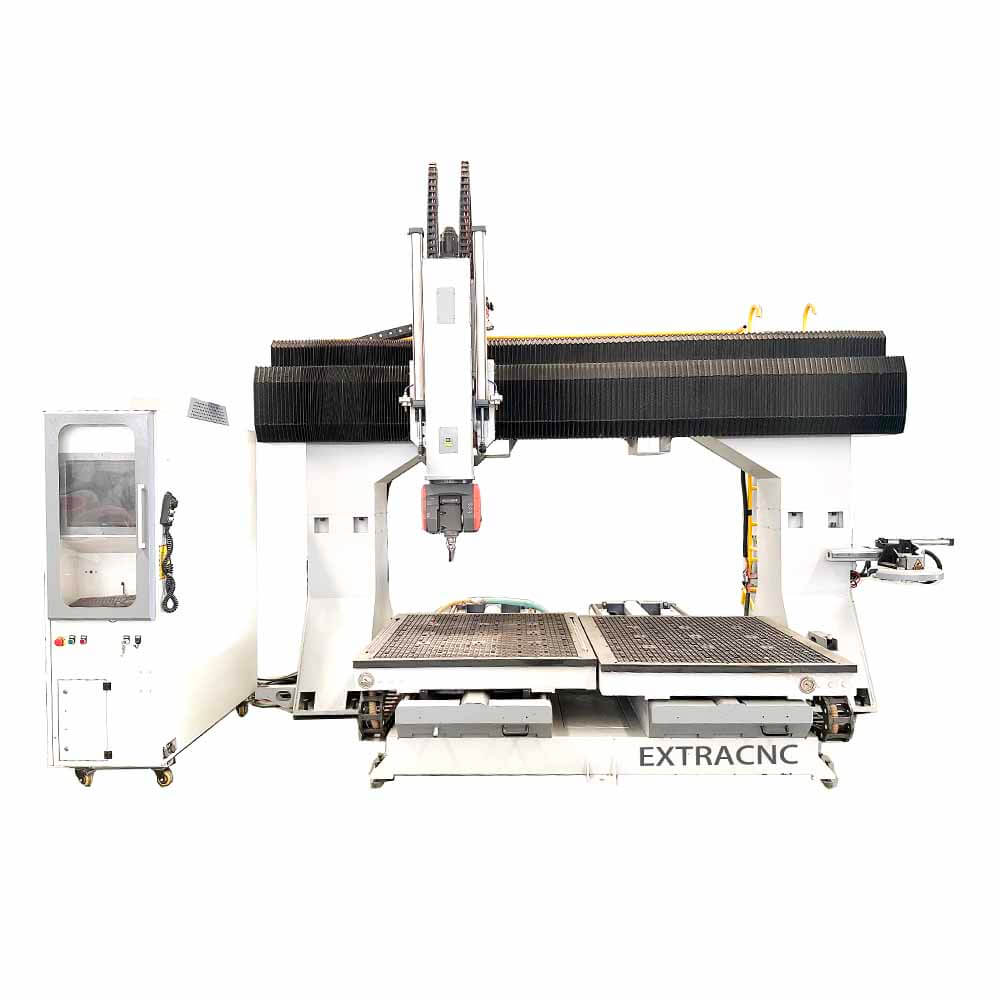
5 Axis CNC Router
A 5-axis CNC router machine is an advanced automated tool that enhances traditional three-axis machining by incorporating two additional rotational axes for five-axis linkage processing. Unlike 3D printers, this technology necessitates a minimum of three linear axes along with two rotational axes, all coordinated simultaneously through a computer numerical control (CNC) system. The 5-axis CNC router comprises several key components, including a Z-axis box, gantry beam, gantry columns, gantry under-frame support, work table, linear ball guide rails, double-turn electric spindle, and servo motors. Its sophisticated gantry-type structure allows for efficient table movement and optimal milling capabilities. During operation, all five axes work together to position the tool in the spindle, facilitating intricate 3D machining around the workpiece. This versatile machine is ideal for cutting and milling various materials, such as wood, plastic, foam, resin, gypsum, aluminum, copper, brass, and carbonized composites, making it valuable in industries like aerospace, automotive, mold manufacturing, and model making.
The Importance of Five-Axis CNC Machines in Modern Manufacturing
In recent years, five-axis CNC machines have become essential tools for machining continuous, smooth, and intricate surfaces. When faced with challenges in designing and fabricating complex curved geometries, many turn to five-axis machining technology for solutions.
Understanding Five-Axis Machining Technology
Five-axis linkage represents one of the most advanced and widely utilized technologies in CNC machining. This method combines computer control, high-performance servo drives, and precision machining techniques, allowing for efficient, accurate, and automated processing of complex surfaces. As a hallmark of a country’s manufacturing technology, five-axis systems play a pivotal role in industries such as aviation, aerospace, and defense.
Navigating the Purchase of a Five-Axis CNC Machine
For many, the decision to invest in a five-axis machine tool can be daunting. Buying a new high-end CNC machine can be exhilarating, but it also comes with substantial financial implications. CNC market reports indicate that the average cost of a new five-axis machine tool approaches $100,000. To ease the purchasing process, consider essential factors such as warranty details, payment options, and post-purchase support. Understanding these elements can significantly simplify your decision-making process.
If you’re aiming to secure the right CNC machine at the best price, you’re in the right place. Whether you’re conducting research or comparing prices, this guide is here to assist you. If you’re ready to purchase now, explore EXTRACNC’s selection of top-rated five-axis CNC router machines listed below.
What is a Five-Axis CNC Router Machine?
A five-axis CNC router machine is a sophisticated multi-axis 3D machining center featuring a CNC controller. Unlike a 3D printer, it is more similar to three-axis and four-axis CNC machines, but with two additional axes of movement. This capability allows for cutting on five edges of the material simultaneously, resulting in shorter project timelines. However, the extended X-axis may lead to decreased stability and accuracy, necessitating more operator attention compared to three- or four-axis routers.
Understanding the Working Principle of Five-Axis CNC Machines
To grasp how five-axis CNC machines operate, it’s essential to understand the concept of “axes”:
- X-axis: Moves front to back.
- Y-axis: Moves left to right.
- Z-axis: Moves up and down.
- A, B, or C axes: Correspond to rotational movements around the X, Y, and Z axes.
In five-axis CNC machining, the tool or workpiece can move along five independent axes simultaneously, allowing for complex geometry manipulation. The five-axis configurations (X-Y-Z-A-B, X-Y-Z-A-C, X-Y-Z-B-C) enable the spindle to rotate 180 degrees, providing comprehensive access to the workpiece from multiple angles.
Five-axis linkage technology specifically pertains to processing complex surfaces that require simultaneous control of five independent axes, ensuring a smooth finish. While three-axis machines can theoretically express any complex surface with X, Y, Z coordinates, actual cutting tools have physical dimensions. Five-axis machining minimizes errors and surface roughness, achieving improvements of up to 1/3 to 1/6 compared to traditional three-axis methods.
Common Types of Five-Axis CNC Machines
There are eight primary types of five-axis CNC machine tools:
- Five-axis linkage machining center
- Five-axis CNC machining center
- Five-axis precision machining center
- Five-axis high-speed machining center
- Small five-axis machining center
- High-precision five-axis machining center
- Five-axis CNC router machine
- Vertical five-axis machining center
Applications of Five-Axis CNC Machines
Five-axis CNC machines are designed to deliver high-speed, high-quality cuts across various materials, including wood, plastics, non-ferrous metals, and composites. Their versatility opens up new applications, including:
Edge Trimming: The flexibility of five-axis machines enables precise finishing and edge trimming for molded plastics and composite parts.
Deep Cavity Mold Making: Unlike three-axis machines that require long tools for deep cavities, five-axis systems allow for the use of shorter tools, increasing cutting speeds and reducing breakage risks.
Molded Plywood Chairs and Decorative Furniture: Five-axis CNC machines facilitate unique shaping and molding, bringing creative and dynamic designs to life.
Intricate 3D Carvings: The enhanced movement capabilities allow for detailed and precise carvings, capturing the fine intricacies of complex designs.
Features of Five-Axis CNC Machines
Five-axis CNC machines are renowned for their high efficiency and precision, allowing for complex machining tasks to be completed in a single clamping of the workpiece. These machines are well-suited for modern mold processing, including applications in automotive parts and aerospace structural components.
Distinguishing Five-Axis and Pentahedral Machining Centers
It’s important to clarify the difference between a five-axis machining center and a pentahedral machining center, as many people mistakenly confuse the two. A five-axis machining center operates with five axes: X, Y, Z, A, and C. This configuration enables five-axis linkage processing, making it adept at handling complex surface machining, special shapes, hollow components, punching, inclined holes, and bevel cuts.
In contrast, a pentahedral machining center functions similarly to a three-axis machining center but can process five faces simultaneously. However, it lacks the capability for special shape machining, beveled holes, and bevel cuts that are characteristic of five-axis systems.
Comparing Five-Axis CNC Machines to Traditional Three-Axis Machines
To appreciate the benefits of five-axis CNC machines, it’s essential to compare them with traditional three-axis CNC machines, which are commonly used in manufacturing. Three-axis machines come in various forms, including vertical, horizontal, and gantry configurations, and typically use methods such as end milling and side cutting.
One key limitation of three-axis machines is that the tool axis remains fixed during machining. This means they can only achieve rectangular coordinates through the interpolation of the three linear axes (X, Y, and Z). As a result, when faced with complex geometries or high-precision requirements, three-axis machines can demonstrate inefficiencies, produce lower-quality surface finishes, and may even be incapable of executing certain tasks.
Advantages of Five-Axis Machining
Five-axis CNC machines overcome these limitations by allowing the tool to approach the workpiece from multiple angles, significantly enhancing machining flexibility and accuracy. This capability leads to improved surface finishes, reduced setup times, and the ability to create intricate designs that would be challenging or impossible with a three-axis setup.
Pros and Cons of Five-Axis CNC Machines
Advantages
One of the key benefits of five-axis CNC machines is their ability to process free-form surfaces that traditional three-axis machines cannot handle, or that require multiple setups to achieve. This capability is essential for manufacturing components such as aircraft engine blades, steam turbine blades, ship propellers, and other complex molds featuring intricate curved surfaces. The flexibility to adjust tool angles during machining allows for the avoidance of tool changes, enabling comprehensive machining in a single setup.
Five-axis CNC milling machines maintain exceptional accuracy and quality when working on free-form surfaces while maximizing efficiency. In contrast, when using a three-axis machine with a ball-end milling cutter to process complex curves, the cutting efficiency is often low due to fixed tool angles, which makes it difficult to ensure a smooth surface finish. However, a five-axis machining center can freely adjust the tool angle, avoiding these issues and leading to higher efficiency and superior surface quality.
When dealing with deeper and steeper cavities, the additional rotational and tilting capabilities of the workpiece or spindle head create optimal conditions for using end mills, reducing the risk of tool collisions with the cavity walls. This feature minimizes tool vibration during machining, enhancing surface quality, machining efficiency, and tool longevity.
Moreover, five-axis machines can complete an entire part’s processing using shorter tools, eliminating the need for reinstallation or the longer tools typically required in three-axis setups. This not only expedites delivery but also results in excellent surface quality.
The technology inherent in five-axis machining centers eliminates the necessity for repositioning workpieces at complex angles, which can lead to multiple setups and adjustments. This saves time and significantly reduces errors, thereby cutting down on the costs associated with fixtures and setup materials.
When comparing five-axis machining centers to their three-axis counterparts, several advantages stand out:
Optimal Tool Cutting Conditions: In three-axis machining, as the cutting tool approaches the edge of the workpiece, cutting conditions can degrade. Maintaining optimal conditions often requires multiple rotations of the table. Five-axis machines can avoid this issue, ensuring better surface quality by maintaining effective cutting angles.
Reduction of Tool Interference: In aerospace applications, components like impellers and blades often face interference issues with three-axis machines. Five-axis systems can meet these processing demands while allowing for the use of shorter, more rigid tools, which reduces the need for specialized tools.
Fewer Clamping Operations: Five-axis machines can reduce the number of clamping setups required by enabling five-sided machining in a single clamping. This simplification enhances machining accuracy by minimizing reference conversions and supporting better process consistency. Additionally, this leads to a reduction in tooling fixtures, floor space requirements, and maintenance costs.
Improved Machining Quality and Efficiency: These machines can utilize the side edges of tools, resulting in higher cutting efficiency.
Streamlined Production Process: The comprehensive processing capabilities of five-axis machines shorten the production process chain, simplifying production management and scheduling. The advantages of five-axis systems become even more pronounced with complex workpieces compared to traditional methods.
Reduced Development Cycle for New Products: In sectors like aerospace and automotive, where new components and molds often feature complex geometries and precise specifications, five-axis CNC machining centers offer the flexibility, precision, and integration necessary to tackle these challenges. This leads to significantly shortened development cycles and improved success rates for new products.
Cons of Five-Axis CNC Machines
Complex Programming and Operation
Programming five-axis CNC machines can be abstract and challenging, posing difficulties for traditional NC programmers. While three-axis machines operate with straightforward linear coordinate axes, five-axis CNC machines feature more complex structures. A single piece of NC code may yield similar processing results across different three-axis machines, but the same code cannot be universally applied to all five-axis machines. In addition to linear movements, five-axis NC programming involves coordinating rotary motion calculations, such as verifying rotation angles, checking for nonlinear errors, and calculating tool rotations. This results in a significant amount of information to process, making the programming highly abstract.
The skills required for operating and programming five-axis CNC machines are interrelated. Adding special functions to the machine further complicates programming and operation. Mastery of these skills demands extensive practice, and a lack of experienced programmers and operators presents a considerable barrier to the widespread adoption of five-axis CNC technology.
High Demands on NC Interpolation Controllers and Servo Drive Systems
The movements of five-axis machines are a combination of the five coordinate axes’ motions. This incorporation of rotational coordinates increases the computational burden for interpolation. Even minor errors in the rotational coordinates can severely impact machining accuracy, necessitating controllers that offer superior precision.
Furthermore, the kinematic characteristics of five-axis machines require the servo drive systems to exhibit excellent dynamic performance and a wide speed range.
Critical Importance of NC Program Verification
To enhance machining efficiency, it is crucial to move away from traditional “trial cutting” calibration methods. In five-axis CNC machining, verifying NC programs becomes particularly vital due to the high cost of typical workpieces. Collisions are common issues in five-axis machining, which can include tool engagement with the workpiece, collisions at high speeds, or interference between the tool and fixtures or other equipment. These collisions are often unpredictable, and the calibration process must involve a thorough analysis of the machine tool’s kinematics and control systems.
If a CAM system identifies an error, it can process the tool path immediately. However, if an error is detected in an NC program during machining, the tool path cannot be modified as easily as on a three-axis machine. In three-axis setups, operators can adjust parameters like tool radius directly. In five-axis operations, such adjustments are more complicated, as any changes in tool dimensions or positioning significantly affect subsequent rotational trajectories.
Tool Radius Compensation Challenges
In five-axis linkage NC programming, while tool length compensation remains effective, tool radius compensation is not applicable. When performing contact-forming milling with a cylindrical cutter, different programs must be created for various cutter diameters. Current CNC systems lack the capability to execute tool radius compensation because the ISO file format does not provide adequate data for recalculating tool positions. Consequently, users must frequently change tools or adjust their sizes during machining. As per standard processing procedures, any modifications to the tool path require recalculation in the CAM system, leading to inefficiencies in the overall processing workflow.
To address this issue, researchers in Norway are developing a temporary solution known as LCOPS (Low-Cost Optimized Production Strategy). This approach transfers the data necessary for toolpath corrections from the CNC application to the CAM system, with the revised toolpath sent directly to the controller. LCOPS necessitates that third-party CAM software be capable of direct communication with the CNC machine, using CAM system files instead of ISO codes. The long-term resolution to this challenge will rely on the development of next-generation CNC control systems that can recognize workpiece model files in widely used formats (such as STEP) or directly interpret CAD system files.
Post Processor
The key distinction between five-axis and three-axis machine tools lies in the inclusion of two rotating axes. This results in the need for multiple coordinate transformations to convert the tool position from the workpiece coordinate system to the machine coordinate system. While popular post-processor generators available on the market can easily generate post-processors for three-axis CNC machines by simply inputting basic machine parameters, the situation is different for five-axis machines. Currently, there are only a few enhanced post-processors specifically for five-axis CNC machines, and further development is needed in this area.
When working with three-axis linkage, the origin of the workpiece on the machine table does not have to be factored into the tool trajectory; the post-processor automatically manages the relationship between the workpiece coordinate system and the machine coordinate system. In contrast, for five-axis linkage—such as when operating a horizontal milling machine with X, Y, Z, B, and C axes—the spatial positioning of the workpiece on the C rotary table, as well as the dimensions between the B and C axes, must be taken into account when generating the tool path. Operators often spend significant time addressing these positional relationships during workpiece setup. If the post-processor could handle this data, it would greatly simplify both the installation of the workpiece and the tool path programming. Operators would only need to position the workpiece on the table, measure its orientation, input this information into the post-processor, and then obtain the appropriate NC program.
Nonlinear Errors and Singularity Issues
The introduction of rotational coordinates complicates the kinematics of five-axis CNC machines significantly compared to three-axis machines. One challenge associated with rotation is nonlinear error, which stems from programming inaccuracies. This error can be mitigated by decreasing the step distance. During the pre-calculation phase, programmers cannot accurately gauge the magnitude of nonlinear errors; these can only be assessed after the machine tool program is generated by the post-processor. Tool path linearization can address this issue, and while some control systems can linearize the tool path during machining, it is typically managed in the post-processor.
Another complication related to rotational axes is singularity. If a singularity occurs at the extreme position of a rotation axis, even minor oscillations near this point can cause a 180° flip of the rotation axis, presenting significant safety risks.
CAD/CAM System Requirements
Effective operation of five-axis processing relies on a robust CAD/CAM system and requires skilled programmers familiar with these systems.
Significant Investment for Machine Tools
Historically, there has been a considerable price disparity between five-axis and three-axis machines. However, adding a rotary axis to a three-axis machine can now match the cost of a standard three-axis machine while providing multi-axis capabilities. Presently, the price of five-axis machines is only 30% to 50% higher than that of three-axis machines.
Besides the initial investment in the machine itself, upgrading the CAD/CAM software and post-processors is essential to accommodate the demands of five-axis machining. Calibration programs must also be updated to effectively simulate the entire machine tool.
Parts & Accessories
Basic Components: These form the foundational structure of the machining center, consisting of the bed, column, and table. They bear the static and cutting loads generated during machining, necessitating robust rigidity. These large components can be made from cast iron or welded steel structures and represent the heaviest parts of the machining center. For instance, AKIRA-SEIKI utilizes high-quality Meehanite castings, which maintain high stability following heat treatment.
Spindle Assembly: This includes the main spindle box, motor, spindle, and bearings. The spindle’s start, stop, and speed adjustments are all managed by the CNC system, facilitating the cutting action through tools mounted on the spindle. As a crucial element of the machining center, the spindle significantly influences both machining precision and stability.
Numerical Control System: The CNC section of the machining center comprises the CNC device, programmable logic controller (PLC), servo drive components, and the operation panel.
Automatic Tool Change System: This system includes the tool magazine and the manipulator drive mechanism. When a tool change is necessary, the CNC system sends an instruction to the manipulator, which retrieves the tool from the magazine and loads it into the spindle. This system automates the storage, selection, transport, and exchange of tools for continuous processing after a single workpiece setup. Tool magazines can vary in design—such as disc or chain types—and can hold anywhere from a few to several hundred tools. The structure of the tool arm also varies based on the configuration of the magazine and spindle, with options like single-arm and double-arm designs. Some machining centers forego a tool arm, instead relying on the headstock or magazine movement for tool changes.
Auxiliary Devices: This category includes systems for lubrication, cooling, chip removal, protection, hydraulics, pneumatics, and detection. While these components do not directly engage in cutting, they are essential for ensuring the machining center’s efficiency, accuracy, and reliability.
Automatic Pallet Change (APC) System: To facilitate unmanned operation or to minimize non-processing time, certain machining centers feature multiple automatic exchange worktables for holding workpieces. While one workpiece is being processed, other tables can be loaded or unloaded. Once processing on one table is complete, the tables are automatically swapped to begin work on new parts, thus reducing auxiliary time and enhancing overall efficiency.
Buyer’s Guide
If you are considering the purchase of a new or used five-axis CNC machine online, it’s crucial to follow a structured approach. Here are ten straightforward steps to guide your online buying process:
Step 1: Budget Planning
Before exploring machine tools, establish a budget. Understanding what you can afford is essential for making an informed choice.
Step 2: Conduct Research
Once your budget is set, determine which machine tool suits your needs. Consider what tasks you will perform with it. Assess your requirements and compare different models and dealers by reading expert reviews online.
Step 3: Consultation
Reach out to our sales manager for guidance. We will recommend the most suitable machine tool based on your specific requirements.
Step 4: Request a Free Quotation
After consultation, we will provide a detailed quotation for the recommended machine tool, ensuring it meets your specifications while staying within your budget.
Step 5: Contract Signing
Both parties will carefully review and discuss all order details (technical specifications and business terms) to prevent misunderstandings. Once everything is agreed upon, we will send you a Proforma Invoice (PI) for contract signing.
Step 6: Machine Manufacturing
Upon receiving your signed contract and deposit, we will commence machine construction. We will keep you updated on the manufacturing progress.
Step 7: Inspection
The entire production process will undergo regular inspections and strict quality control. The complete machine will be thoroughly tested to ensure optimal performance before leaving the factory.
Step 8: Shipping
Shipping will proceed according to the terms outlined in the contract after your confirmation. You can request transport updates at any time.
Step 9: Customs Clearance
We will provide all necessary shipping documents to facilitate smooth customs clearance.
Step 10: Support and Service
We offer professional technical support and complimentary customer service via phone, email, Skype, WhatsApp, online chat, and remote service. Additionally, door-to-door service is available in select areas.